
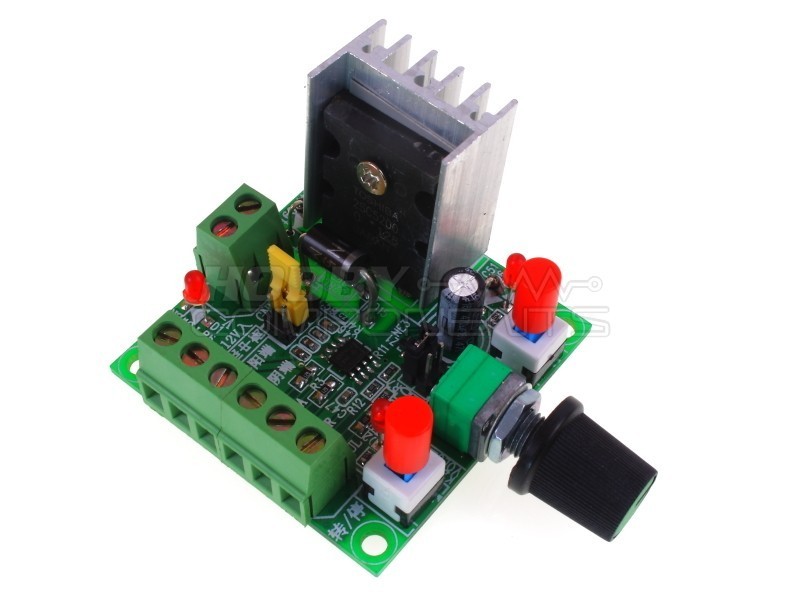
When voltage is applied across an RL circuit, the inductor opposes current through the circuit. To analyze the radiation effects as the radiated electromagnetic energy is generally higher with PWM whenĬompared with DC linear sources. While using PWM to drive the motor where EMC (electromagnetic compatibility) is critical, it is recommended The presence of back EMF along with the RL circuit in a brushed DC motor brings non-linearity to the PWMĬontrol and both the PWM frequency and PWM duty cycle become significant for optimal output power. When the motor is running at moderately high speed, the back EMF is comparable to the applied voltage, soĪ component representing the back EMF needs to be added to the equivalent circuit.
#Pwm driver circuit for stepper motor free
The presence of the free wheel diode allows the charge to dissipate 2 should never be omitted while using a varying voltage suchĪs in the case of PWM driving the motors. The free wheel or snubber diode shown in Fig. When the motor is at rest or rotating at a very low speed, the back EMF can be neglected and a simplifiedĮquivalent circuit of the motor is shown (Fig. ThisĬomplicates the design of a PWM circuit as not only the duty cycle but the frequency of PWM needs to beĬontrolled precisely for optimum motor performance. Moreover,Ī back EMF, equivalent to motor characteristics (KE) and speed, is generated across the terminal. In addition to the Ohmic resistance, a DC motor winding offers inductance to the PWM circuit. Portescap catalog values and life tests results are derived with a constant linear DC power supply. The inductance does not affect the current as at constant source, the impedance 1 shows an equivalent circuit of a motor driven using a linear DC source. Linear Versus PWM Power Supply LINEAR DC SOURCEįig.
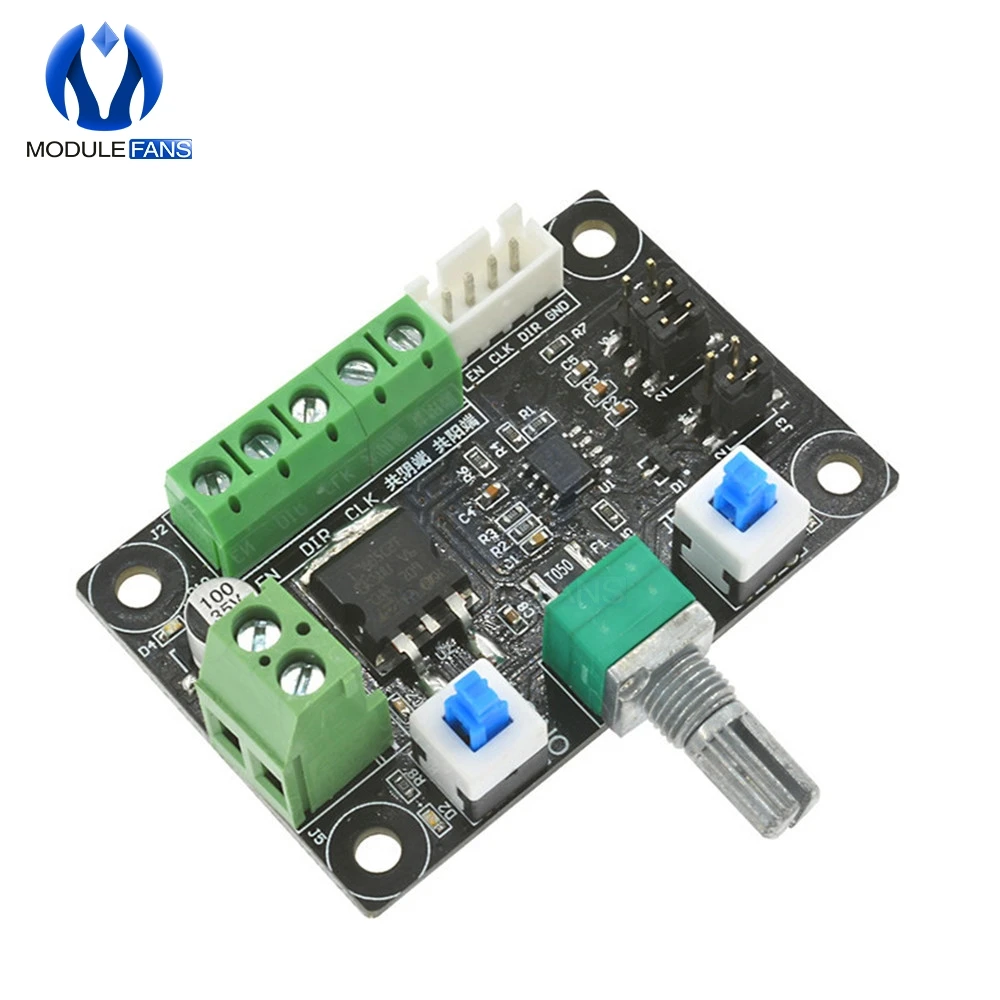
Unlike a pure resistive load, for a DC motor, the resistance, inductance and back EMF on the rotor windings are deciding factors for optimizing PWM frequency and duty cycle. Torque, which is linearly proportional to the average winding current, canīe correctly controlled thanks to our coreless design. Use of PWM enables current control in the windings. This enables use of the motor in anĪpplication where dynamic behavior and fast responses are desired. Portescap brushed DC motors offer very low inertia and low inductance. With a proper design of PWM, the eddy current effects can be minimized, allowing the motors to be optimally The continuous PWM switching, which in general, is not present in the case of a linear power source. One trade-off of using PWM with a motor is the appearance of eddy current losses in the rotor windings due to Reduces the heating of the electronic components.

The improved efficiency of the PWM drive increases battery life and
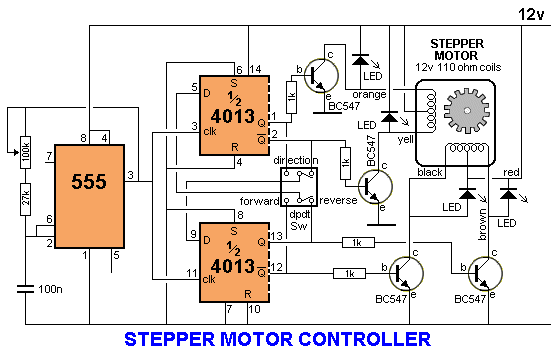
PWM voltage regulation, on the other hand, is efficient and can be used effectively withīattery or DC power-driven applications. Moreover, in battery-driven applications, it becomes impractical to use the linear regulation at The linear regulation is generally inefficient and demands increased Running the motor at usable load points requires a variable,Ĭontrollable power source, which can be achieved through continuous linear regulation power supplies or One load point or through specific load cycles. Many applications utilizing Portescap’s brushed DC miniature motors demand driving the motors at more than
